While ago, I have made a cooling pad for my gaming laptop. It features 3 fans in which two blow air upwards and one blows downwards. This way, the airflow maintains under the laptop chassis. Depending upon how the laptop heats up, its own fans should suck the cool air to cool its components down and as you know; if the temperature gets too high inside a computer, it underclocks itself to protect the components from burning.

Unfortunately, this is the problem that I was facing. During the gaming session, the laptop heats up so easily without a cooling pad of course so that the CPU frequency gets lower than its actual base frequency. As a result, I get a huge FPS drop in the games. So, here, in this article, I have described how to cool the laptop properly by constructing your custom back cover.
Read More: How to Build an Android TV Box With a Raspberry Pi 4?
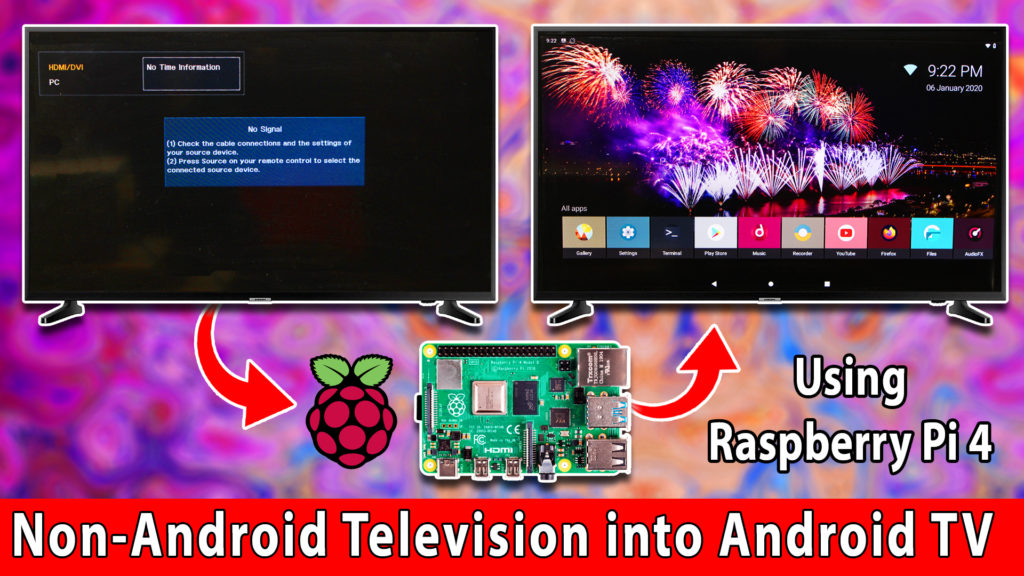
Why is a Cooling Pad so Necessary?
By the way, the laptop what I am using has Intel core i7 7700HQ CPU which base & boost clock are 2.8 & 3.8 GHz respectively and GTX 1060 MAXQ graphics card which has a base & boost frequency of respectively 1063 & 1480 MHz, obviously these components are pretty powerful for a laptop.
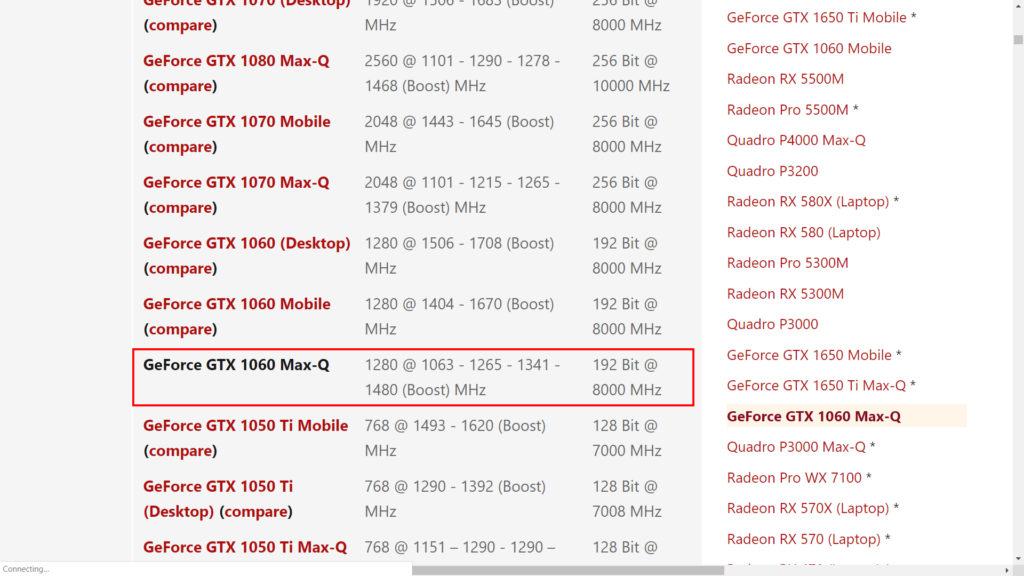
Because their space is limited, providing a big cooling solution is obviously not possible. So, you guessed it, the laptop will be getting warm and warm when it will be at heavy processing-intensive tasks and it is not ignorable that the environment is pretty warm most of the time here. So it will affect the whole system.
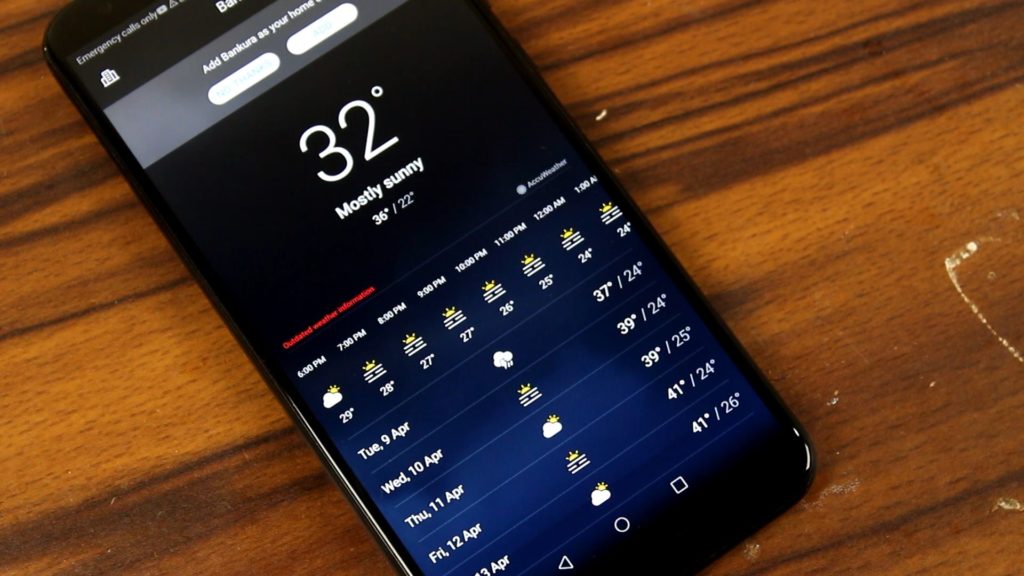
With that cooling pad, this heating issue can be minimized if I removed this cover of the laptop otherwise with this small ventilation, the air flow hampered too much to show its power. Also, this direct airflow directly hits the components especially to these heat pipes which carries the heat of the CPU and GPU towards this heatsink. I do not have to mention that sacrificing the back-protection cover is obviously dangerous. Any kind of material like very small metal piece or screw or may be the dust can enter into the laptop circuitry and also the fans collect more dust as they normally do.
Idea Construction of Making the Cooling Pad!
After thinking of a while, I have come into this idea. A simple board that fits in the place of back cover. The board consists of 4 circular cutouts – two are for the laptop fans. This throws the cool air to the heat pipes if I used this laptop on a cooling pad and the last one is just for more ventilation. Finally, to protect all of these holes, we have to use some sort of mesh and later to fit the whole contraption in which using some screws and hinges are obviously necessary. After putting the theory and conceptual drawings out of the way, let’s start with the actual build.
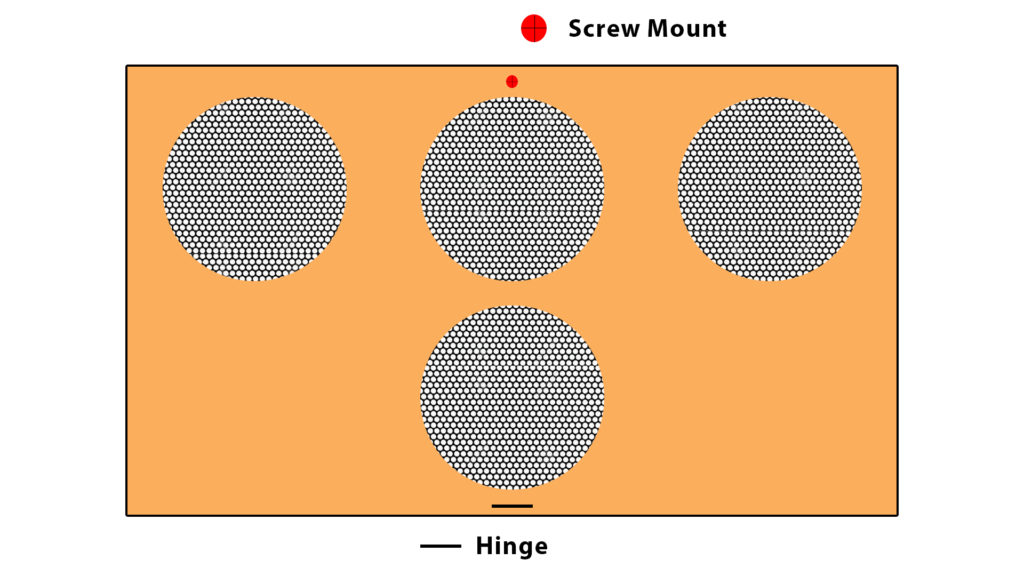
Setting up the Basic Structure of the Cooling Pad
So, I took an 0.5 mm thick MDF board and started to take out our required piece for this project. For that, I have used the laptop’s original back cover as a reference.
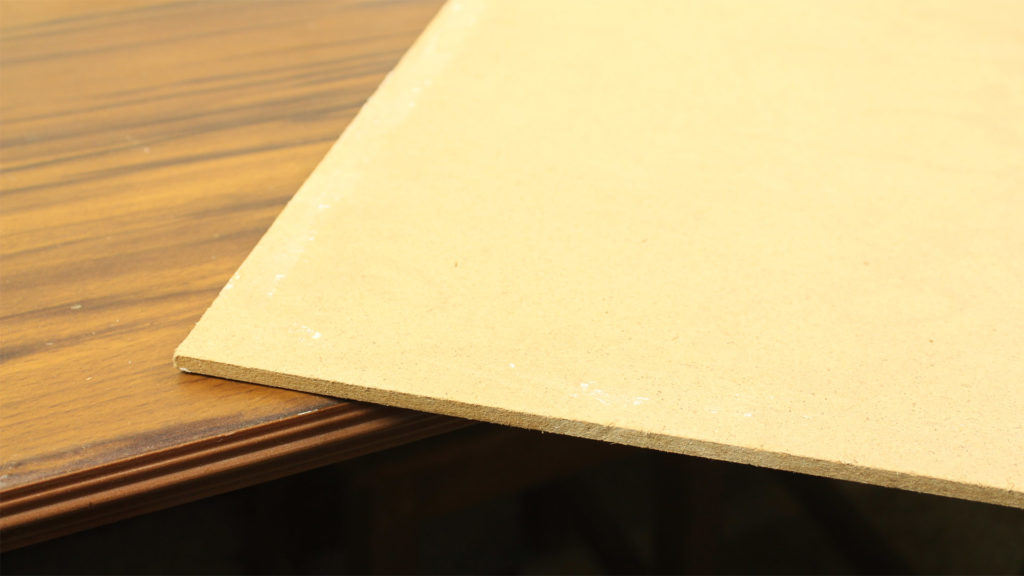
After tracing its dimension, I have used my square ruler to verify it. Then I have used my circular saw to cut off the extras.
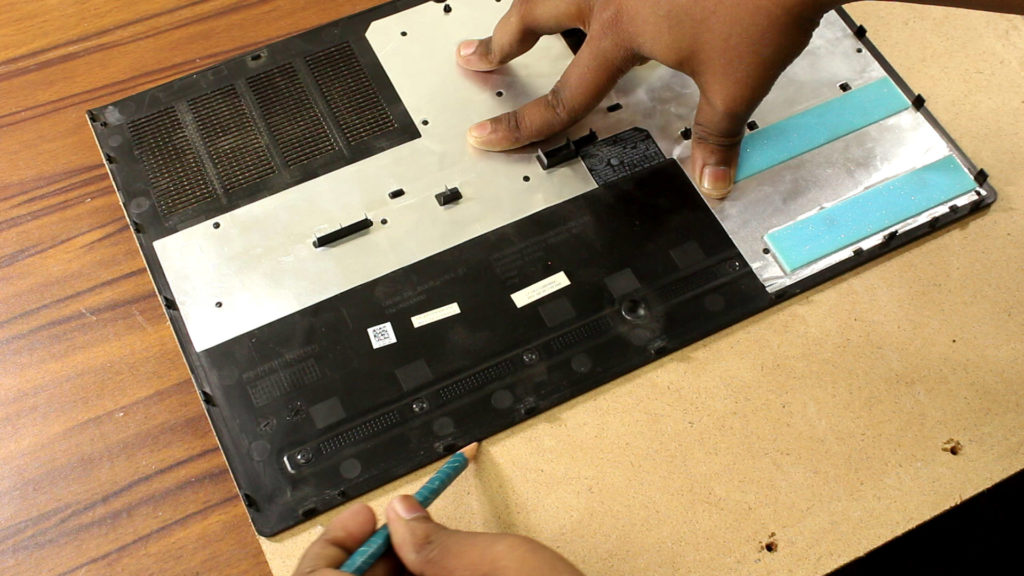
Cutting with the circular saw is a little bit tricky here. First, I have adjusted the cutting depth in the saw which was pretty shallow at the first chance, the blade here barely touches the material.
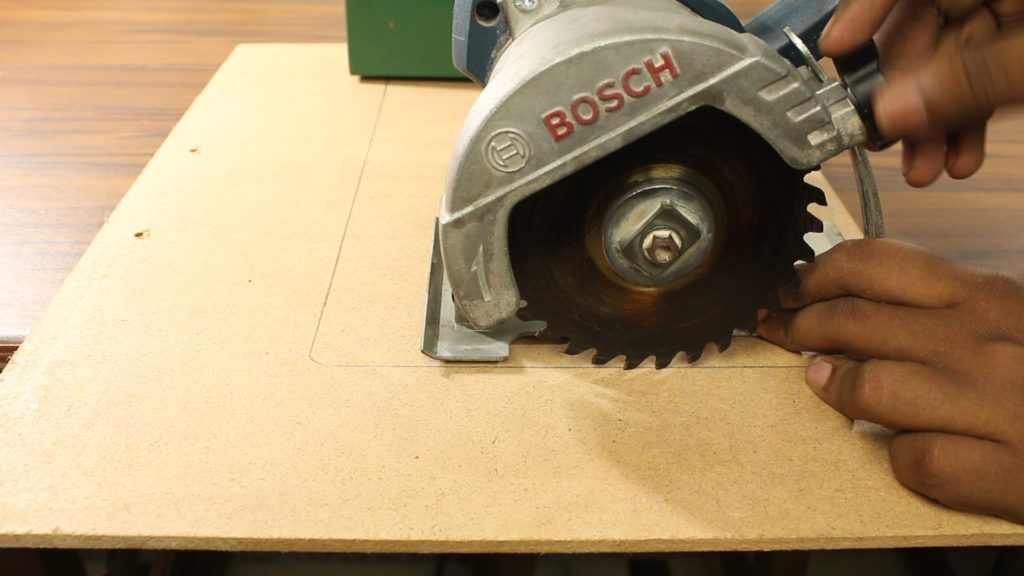
To get accuracy in the saw movement, I have used my ruler as a reference and fix the ruler with some heavyweights from both sides. This way the ruler does not move and helps me to maintain the saw in a straight line.

After getting our required piece I have placed the MDF in the back-cover’s cavity.
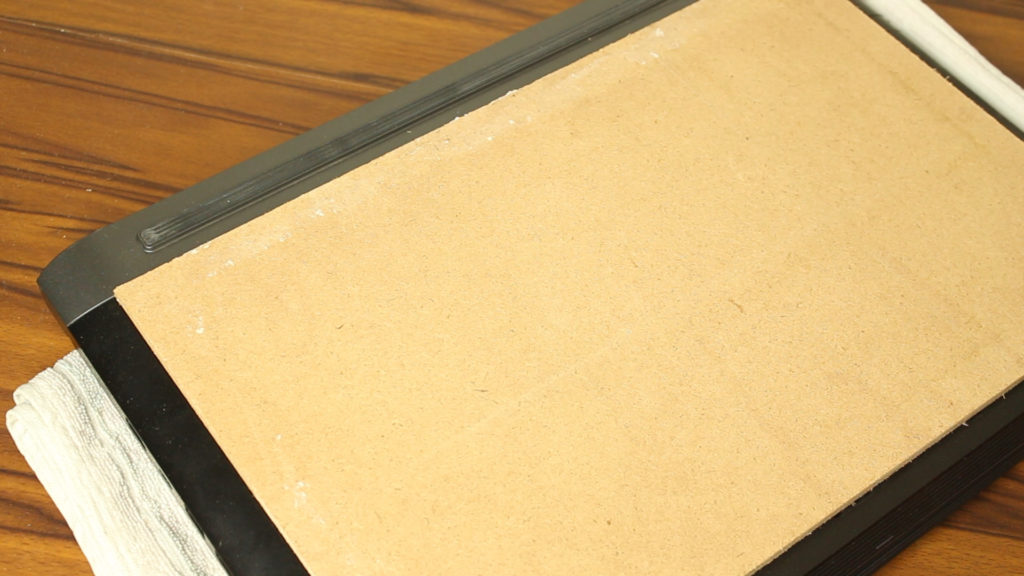
For better finishing, I have trimmed down the edges with a bit of file treatment.
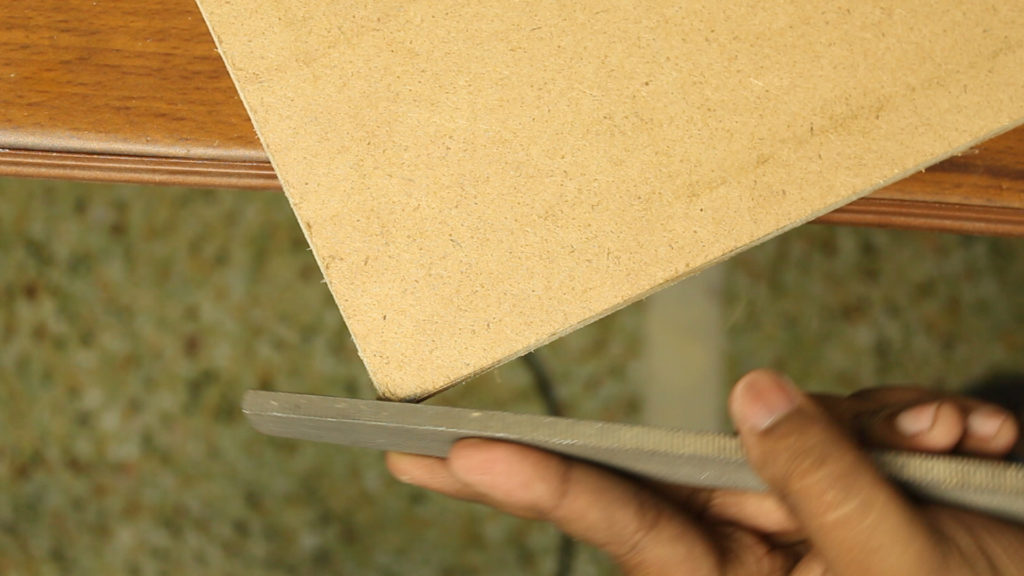
And as a reference, I have once again use the original back cover of the laptop.
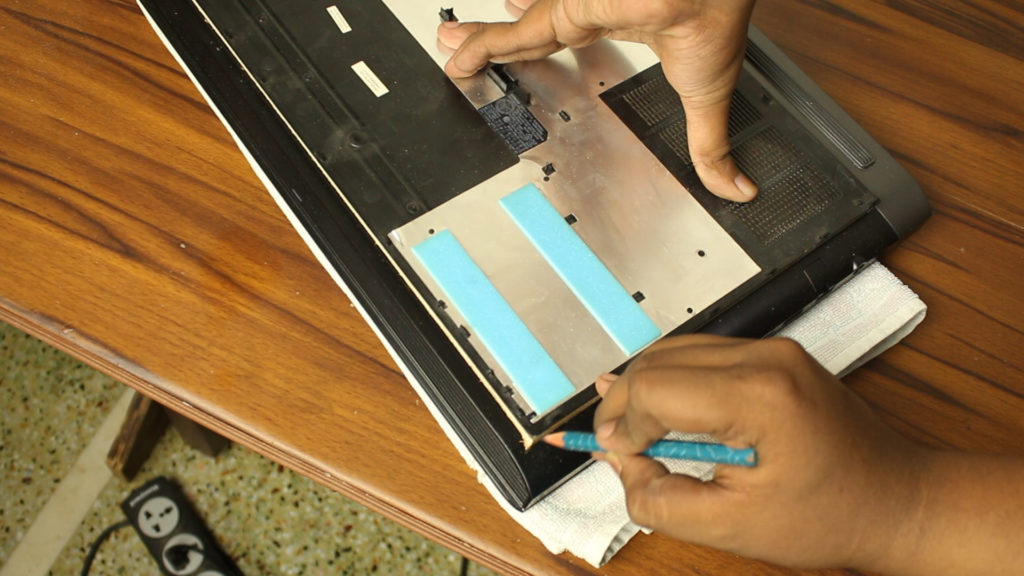
Constructing the Primary Cutouts
After completing the basic structure, we need to construct the laptop’s fan intakes and other ventilation cut outs. For that, I measured the actual size of the original cover and got these results. From the top, left, right and from the bottom I got 1.5, 1.5, 1.5, and 15.5 cm, respectively.
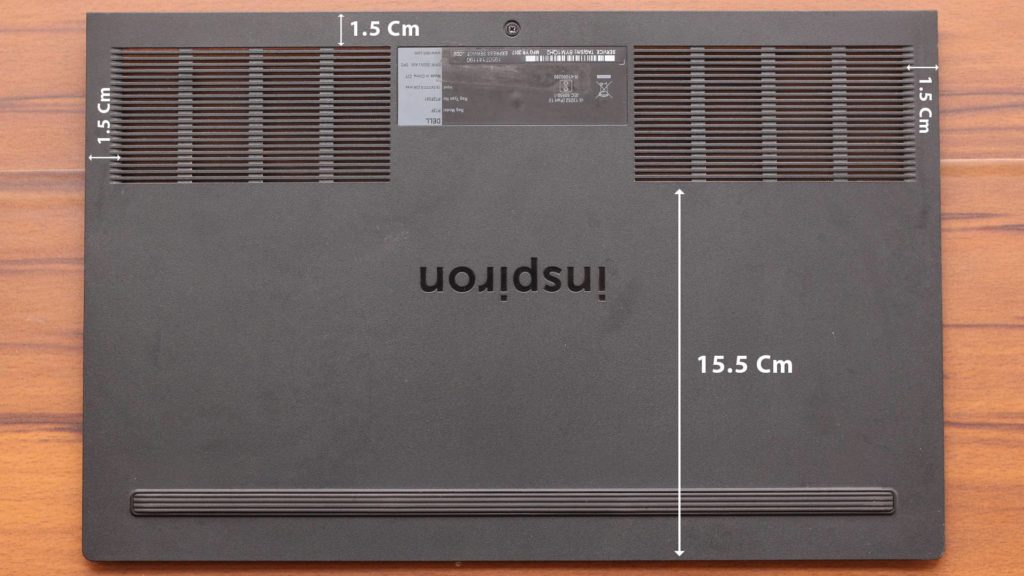
To keep these values in mind and by tweaking some of the values here and there, the values look like this.
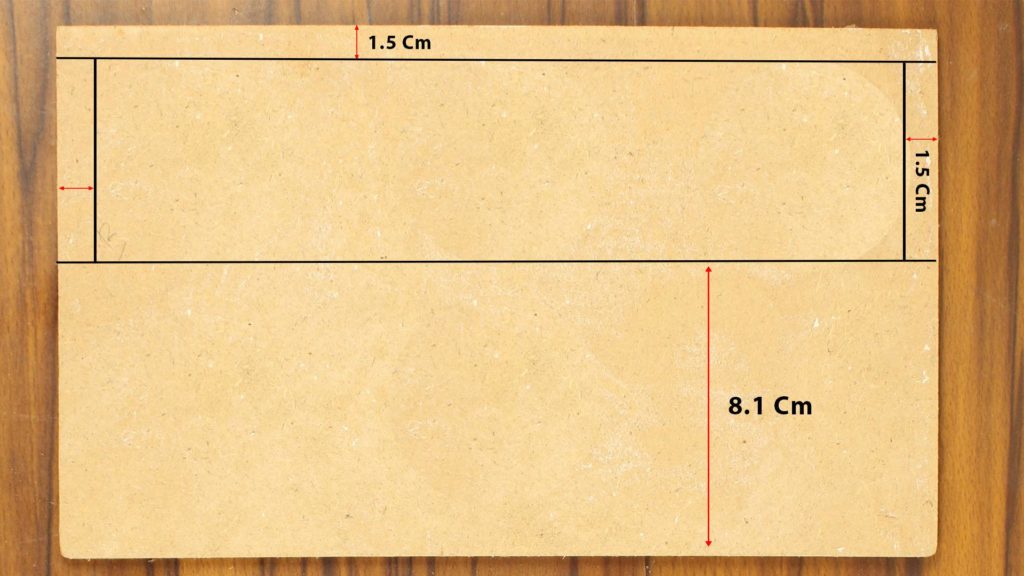
By following that measurement, I have marked both sides and joined them using my square ruler so that a straight line occurs and with this same technique, I have drawn the other lines on both sides. When it was done, I have marked at a distance of 8.1 cm from the bottom, and using my square ruler, I have completed the first set of straight lines.
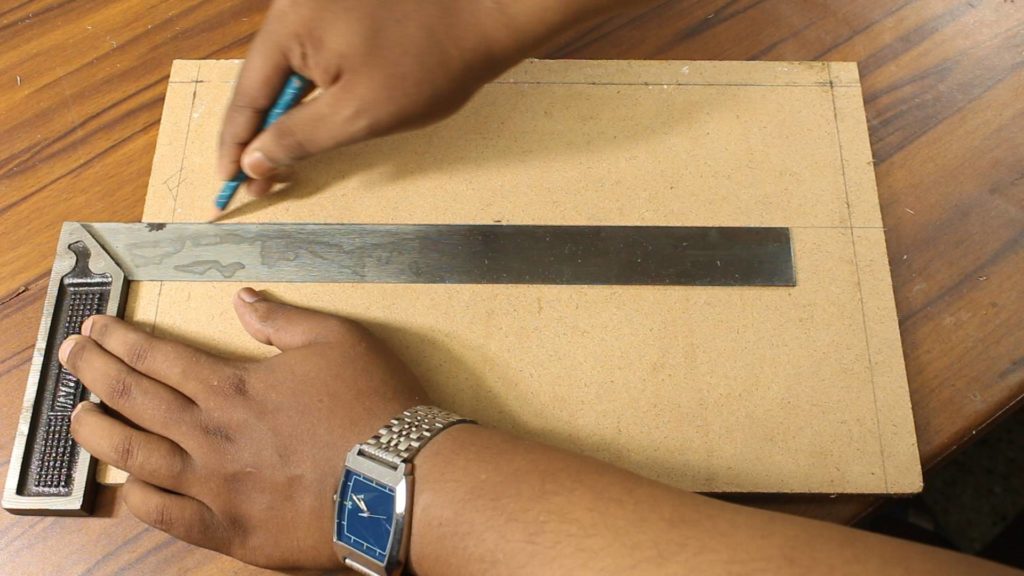
Next by verifying the distance between them, I have found the center positions which are at 4.05 cm. This madness is done 2 times.
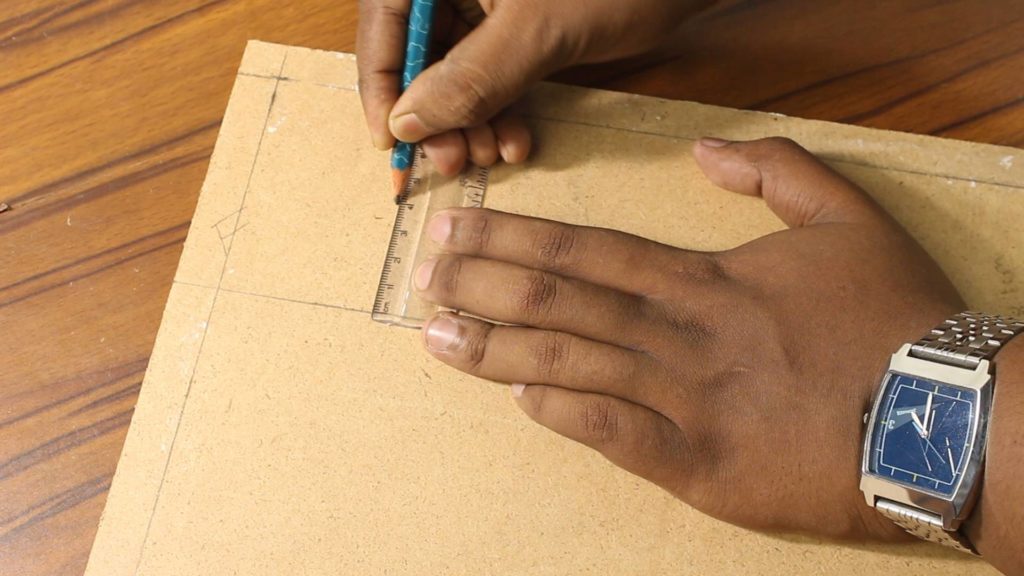
Again, to join the 3 marks, the square ruler comes very handy.
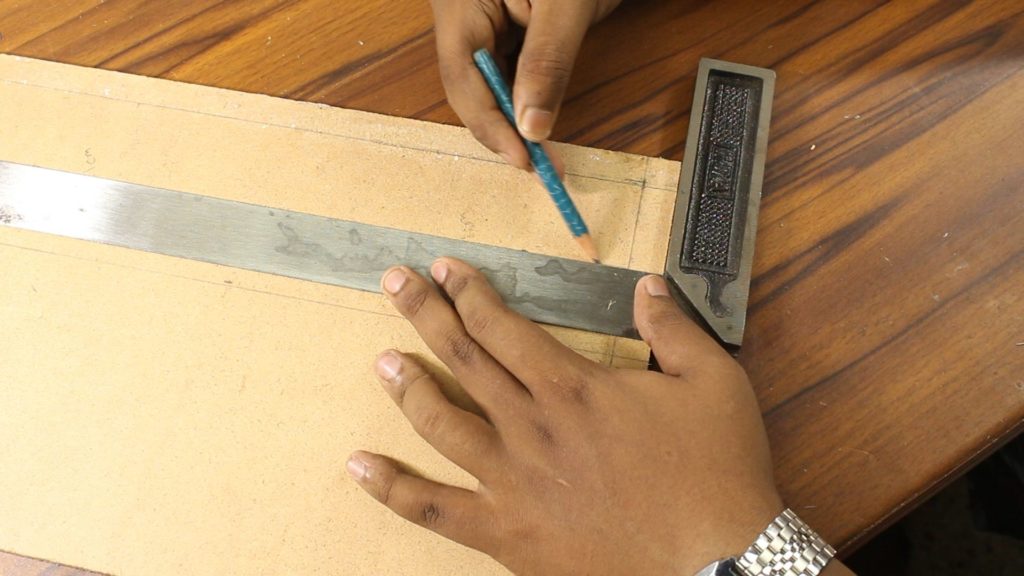
Next, I have marked 4 cm away from the side reference and drilled a pilot hole with a 6 mm drill bit.

Then by using that pilot hole, I made a circular hole with my 3-inch hole saw. After repeating this process on the other side, I have completed all the fan intake cutouts on the MDF.
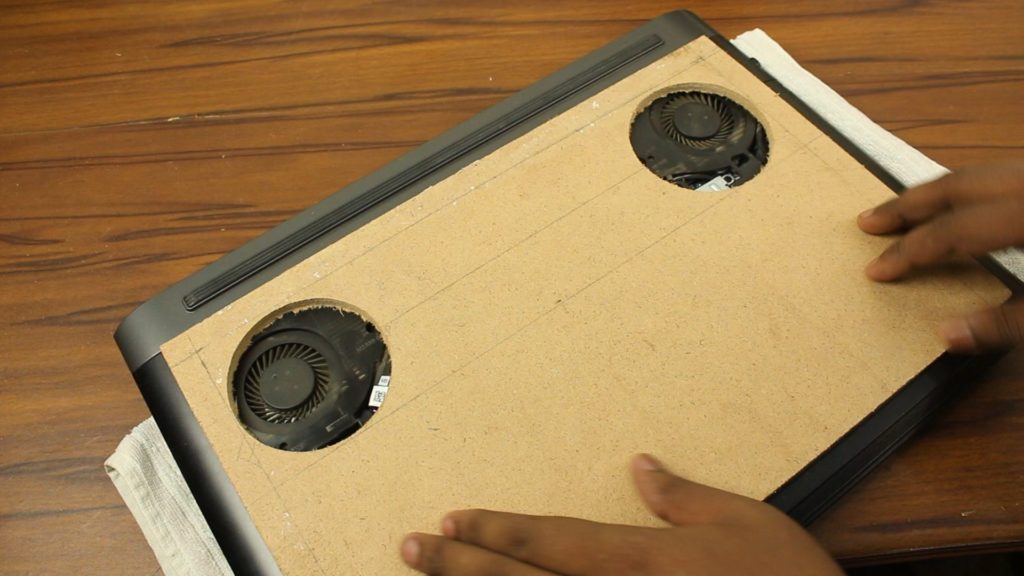
That’s not all, here are two heat pipes which carry the heat of the CPU and GPU to the heatsink. If we cool them down then transferring heat to the heatsink can be minimized.
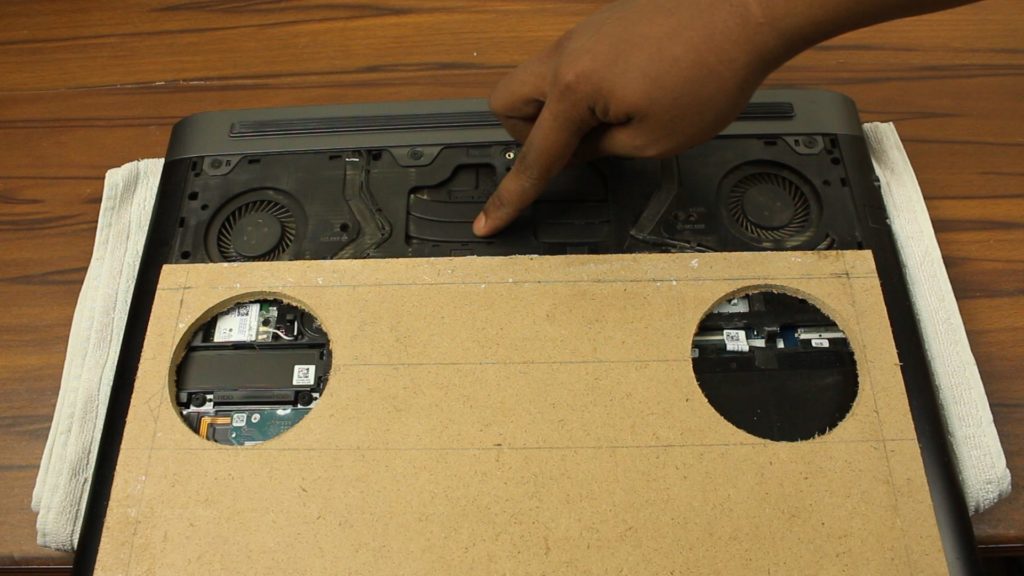
So, without further ado, I made a circular hole on the MDF by following the heat pipes position.
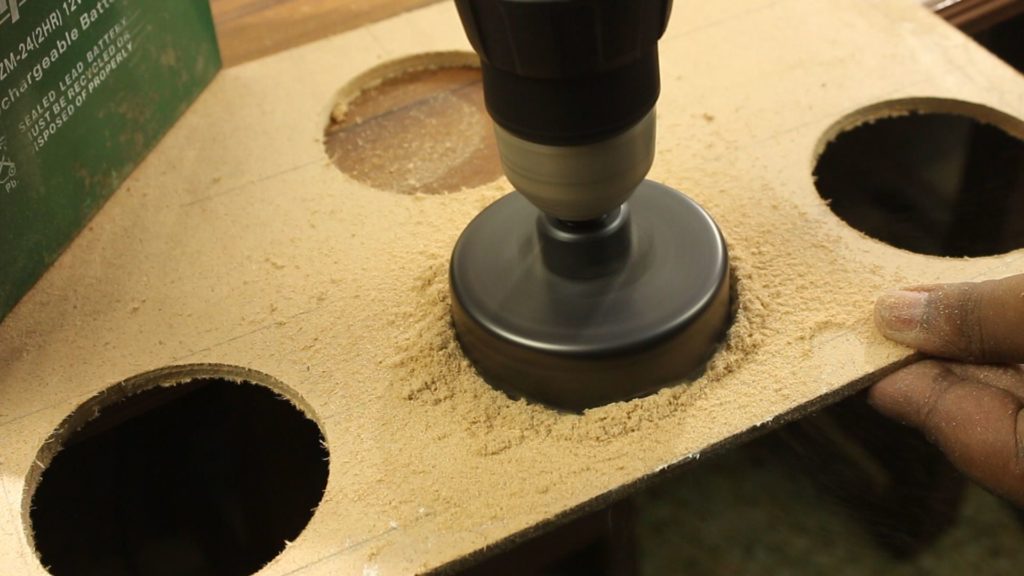
To improve the airflow a bit, I made another hole in the bottom.
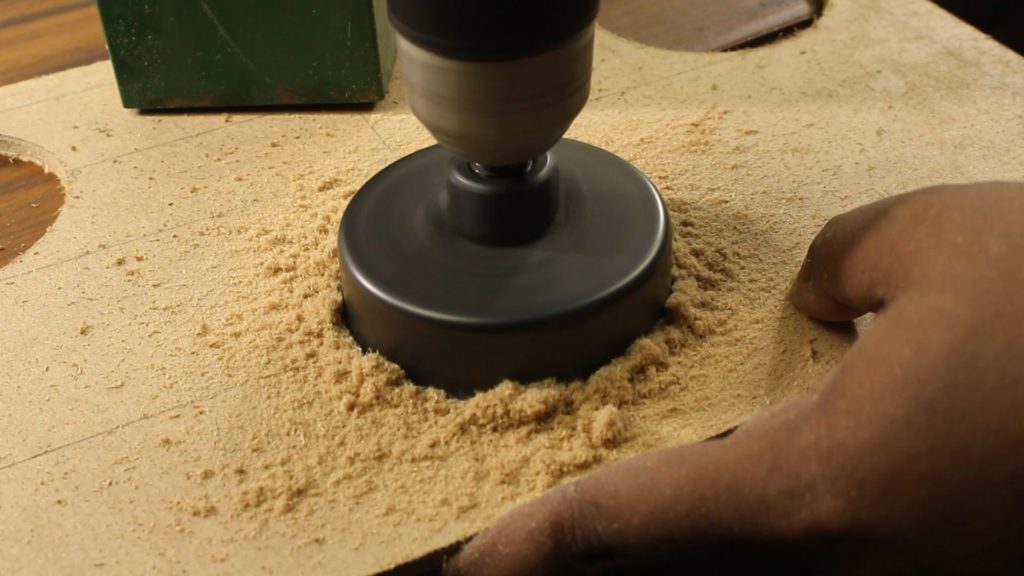
For these cuts, first I have measured the size of the board, found its center, and using my square ruler, I made a straight line by following the center mark.
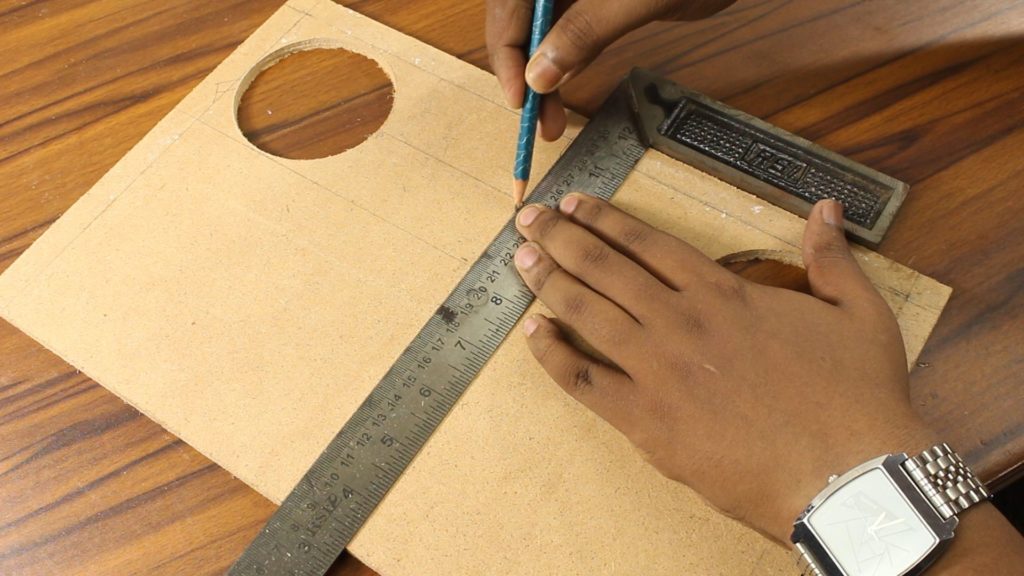
Next, I have stretched the line to the bottom of the board. then I have found the center of the stretched line which is around 6.2 cm and marked it.
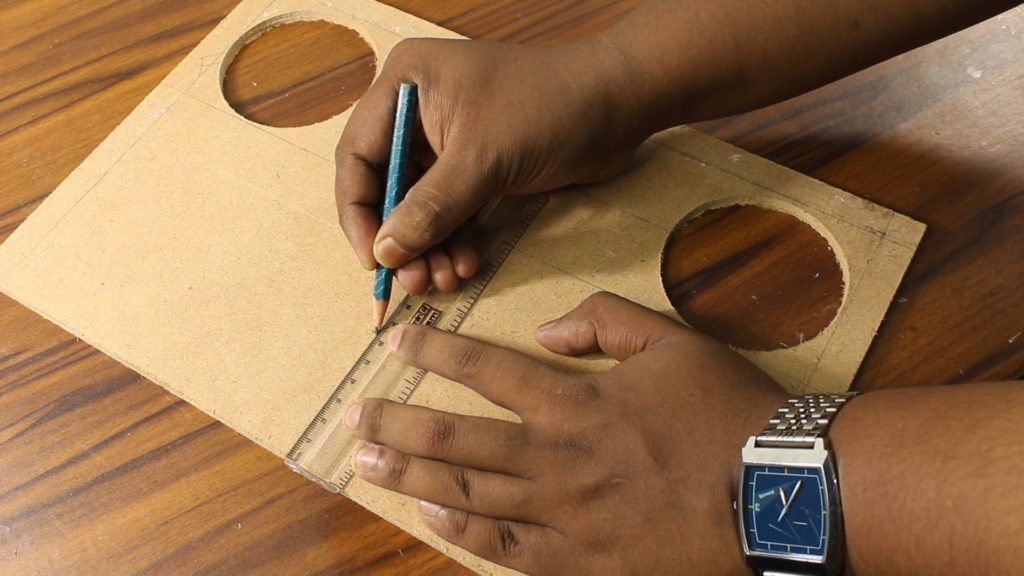
by following that marks, I have drawn a straight line to guide the drill bit.
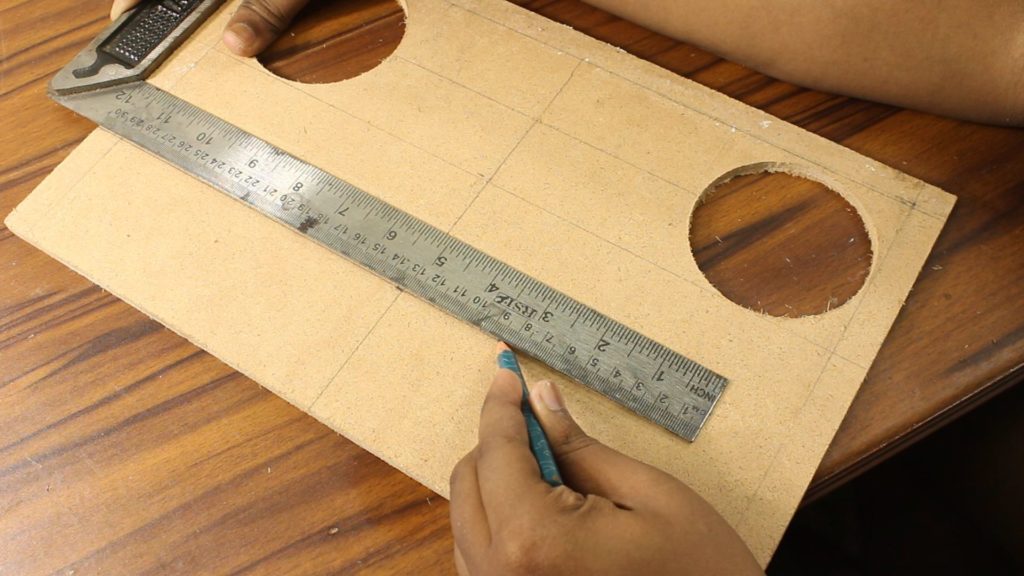
Then I made pilot holes to run the circular saw through the MDF. As I said before, if we left this contraption like this – it could be very dangerous for the laptop so I found a metal mesh on my racks. Anyway, through the gaps of this mesh, air can easily flow but dust and other stuff are kind of resisted.

To set this mesh, I flipped the MDF > left 1.2 cm & 12.5 cm from the top & bottom > drew straight lines on both sides by following that guidance.
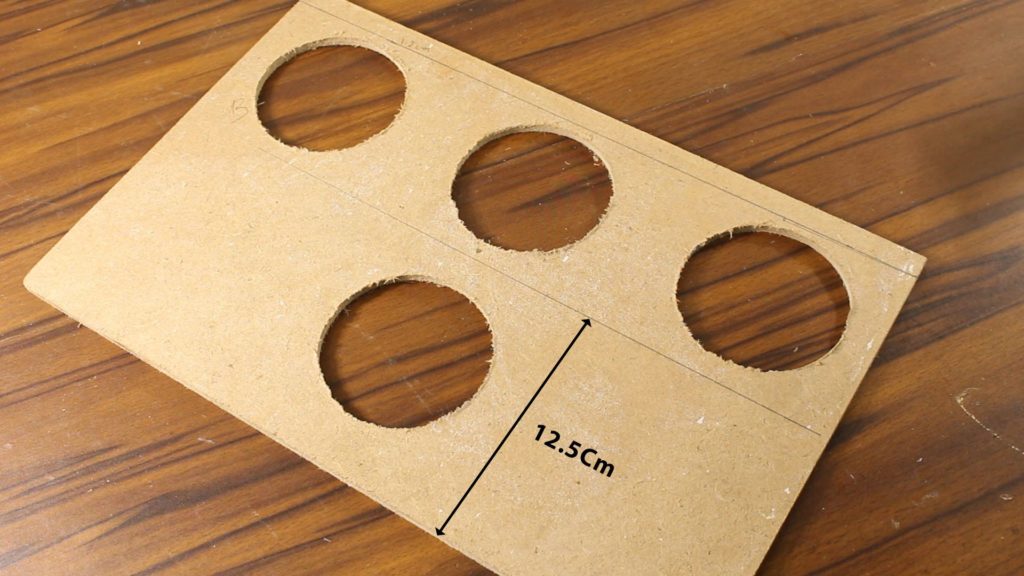
Then, I have maintained a cm distance from the edges > marked them & completed the rectangle.
Then for the bottom one, I followed almost the same way but this time the only difference is the 1 cm gap is counted from the circular cut out not from the edges.
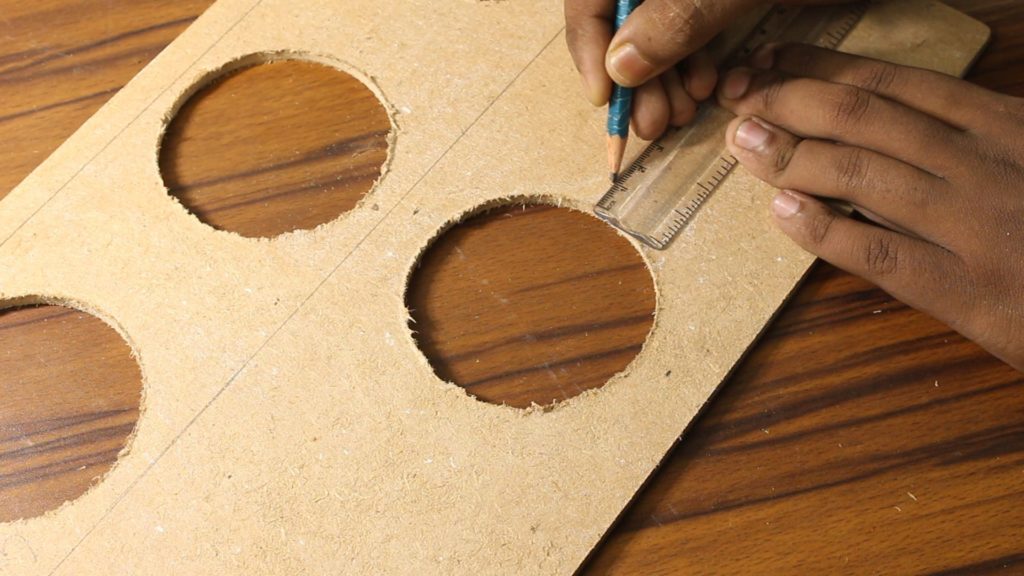
It seems stupid though but to avoid mistakes I have marked all the positions where I have made the grooves for the mesh.
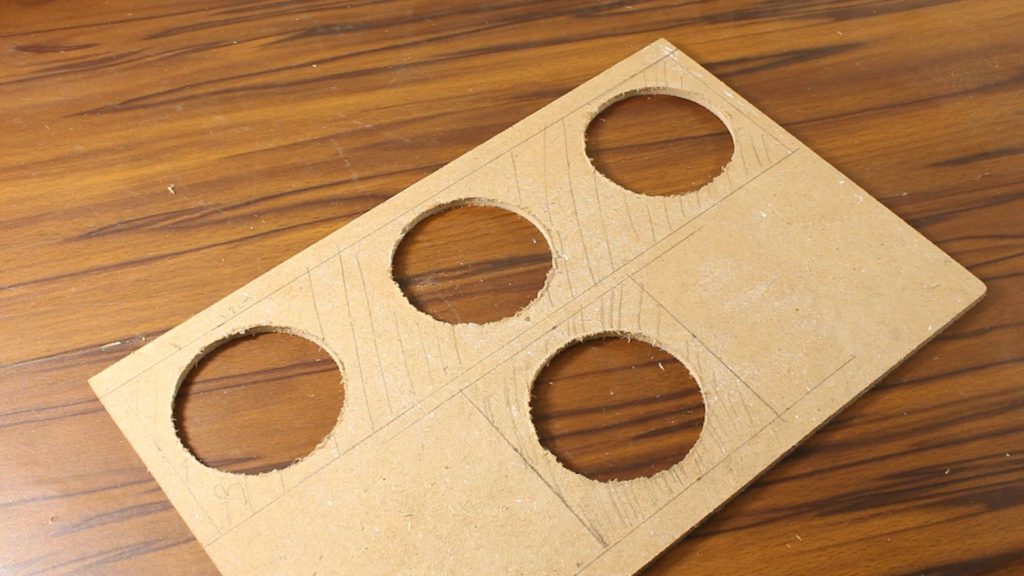
Next, I have taken my circular saw > adjust its cutting depth and ran the saw by following the outlines.
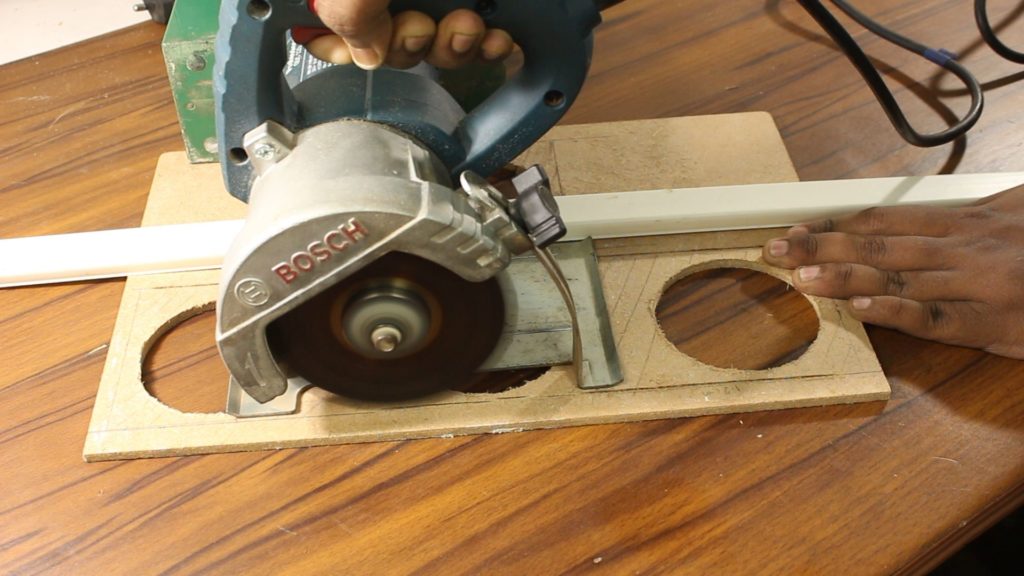
Then, I ran the saw randomly inside the outlines.
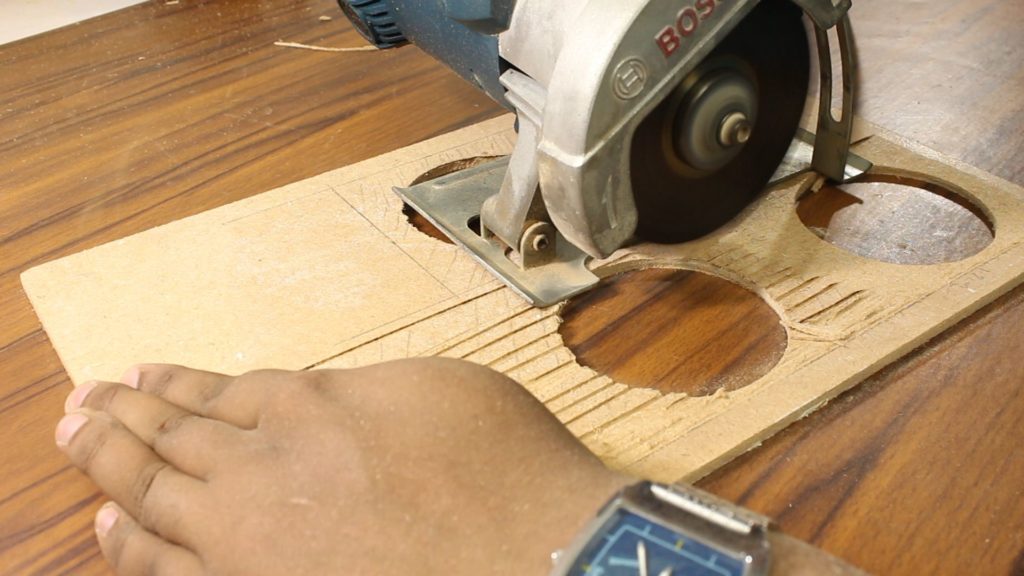
To finish this up, I have used Grid 80 Sandpaper to smooth the surface down.
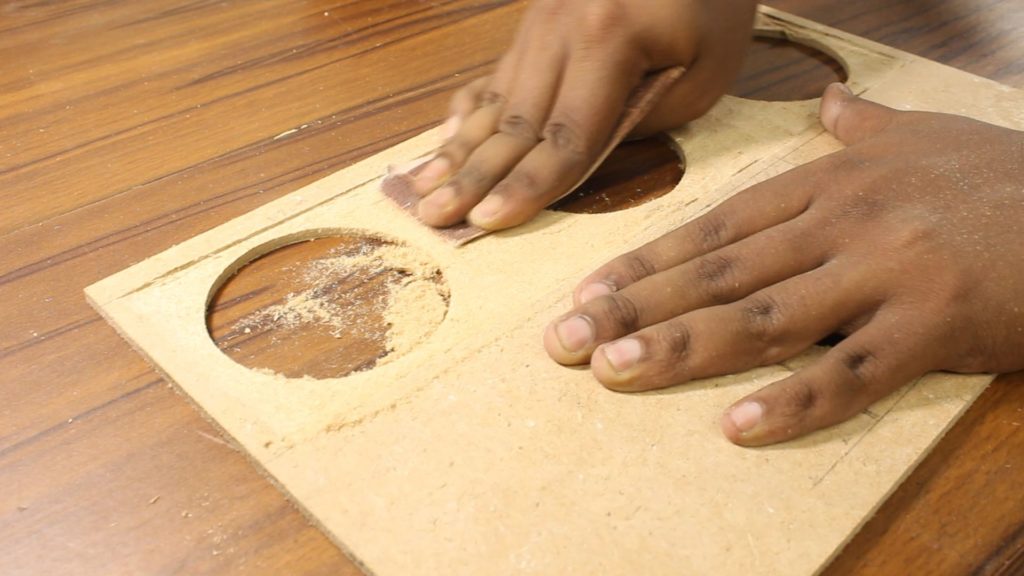
Then I have marked on the metal mesh and snipped off the extras with my rotary tool.
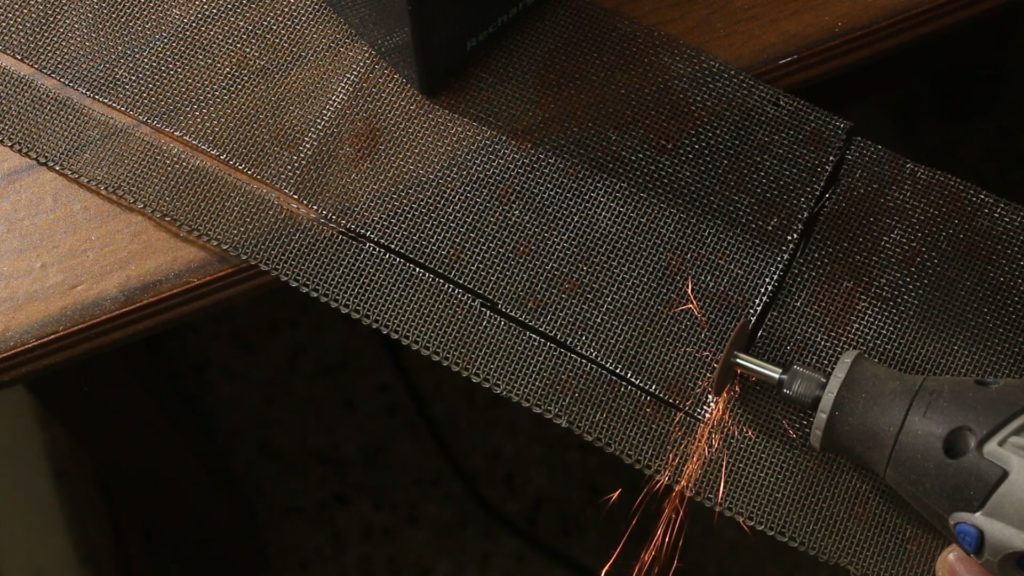
For the last cut, at first, I moved my circular saw through the outlines and then moved the saw diagonally and then using chisel, I took out the layers and sand down the extras.
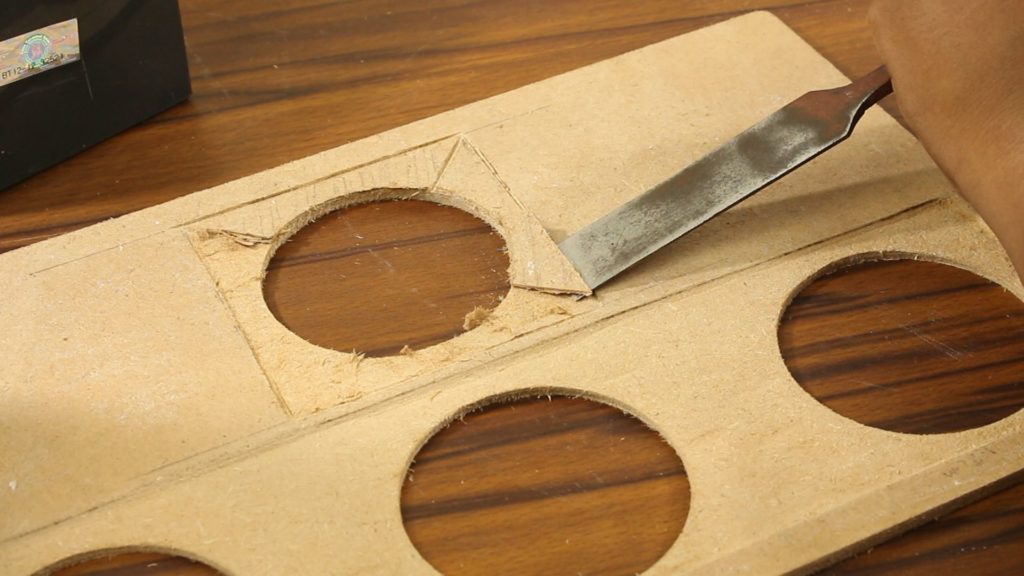
Lastly, for this opening, I have snipped off another piece of the mesh using my rotary tool. Done. Now As obvious, both the meshes are perfectly fitted on their places but it looks a bit misaligned because over the years it is bent a bit although this problem will be solved later when I glued them with the MDF.
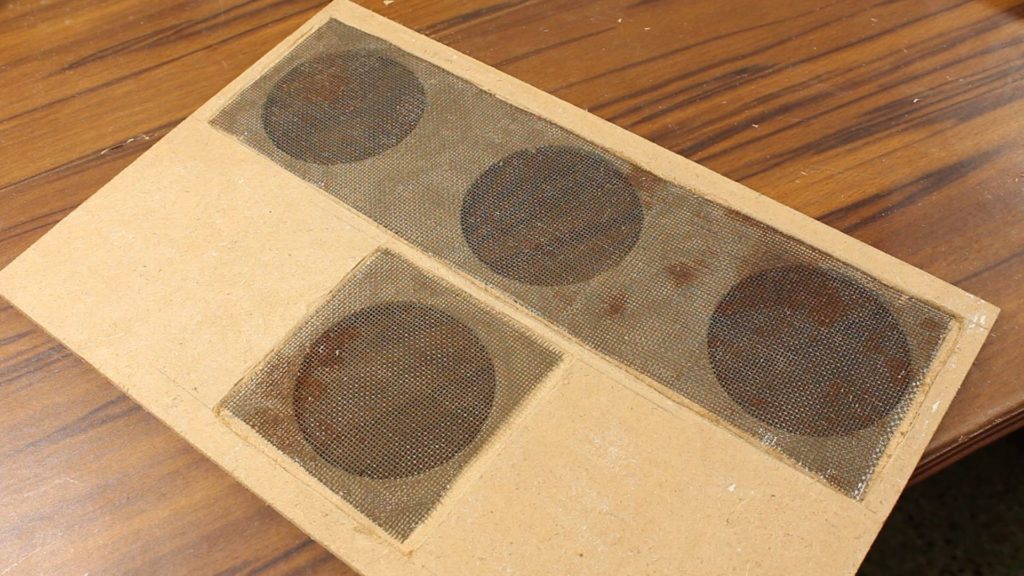
Building other Important Accessories
Anyway, to fit this hole contraption I made a hinge on the bottom and a screw on the top. Actually, this design is obviously taken from the original one. Though there are many hinges on their design but to keep this project simple, I made only this bottom hinge.
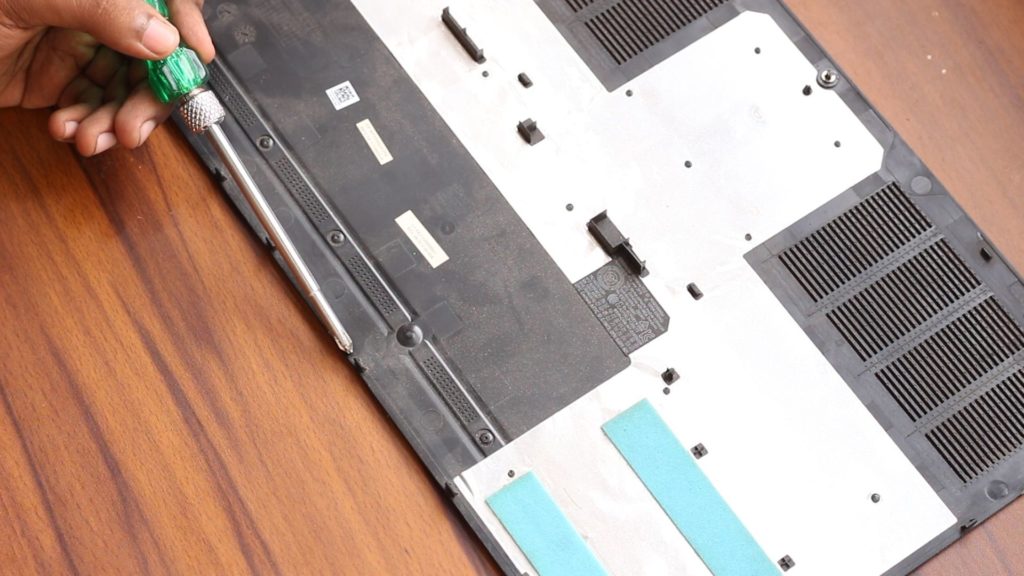
To construct it, I drilled a hole with a 1.5mm drill bit which was almost in the middle of this line but during the drilling process, I have slid my drill a bit for further alignment.
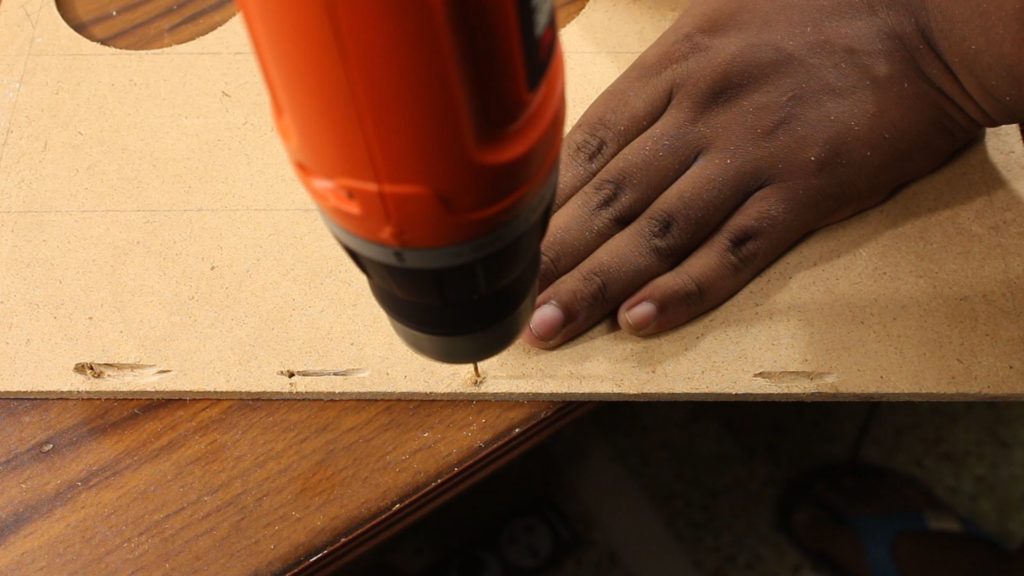
Then, I have used 17SWG copper wire to make the hinge.
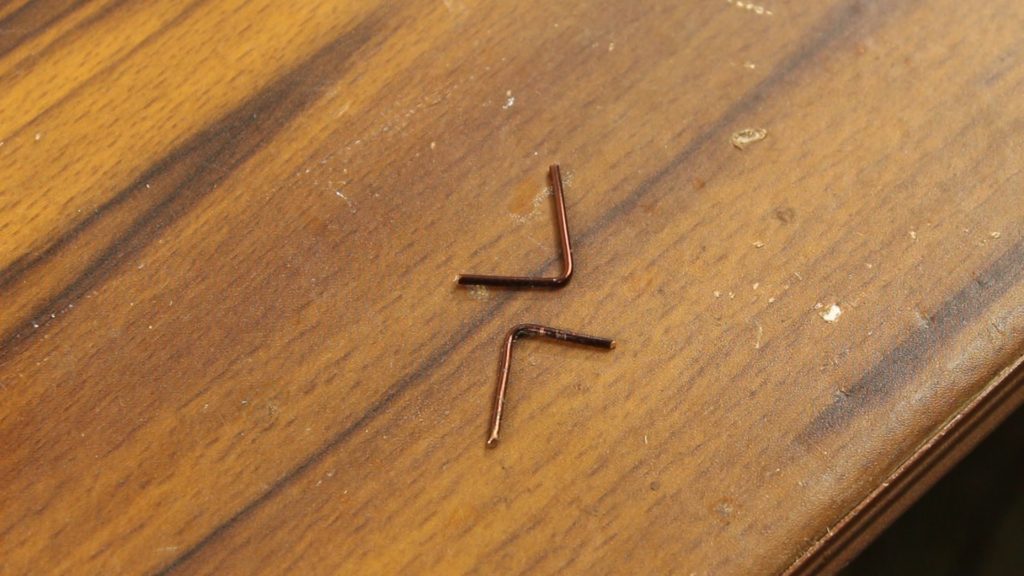
I am not mentioning the size now because we need to sniffed off extras later. then I have bent the wire 90 degrees > cut grooves beside the drill and hammered the hinge through the hole and slightly bent it again.
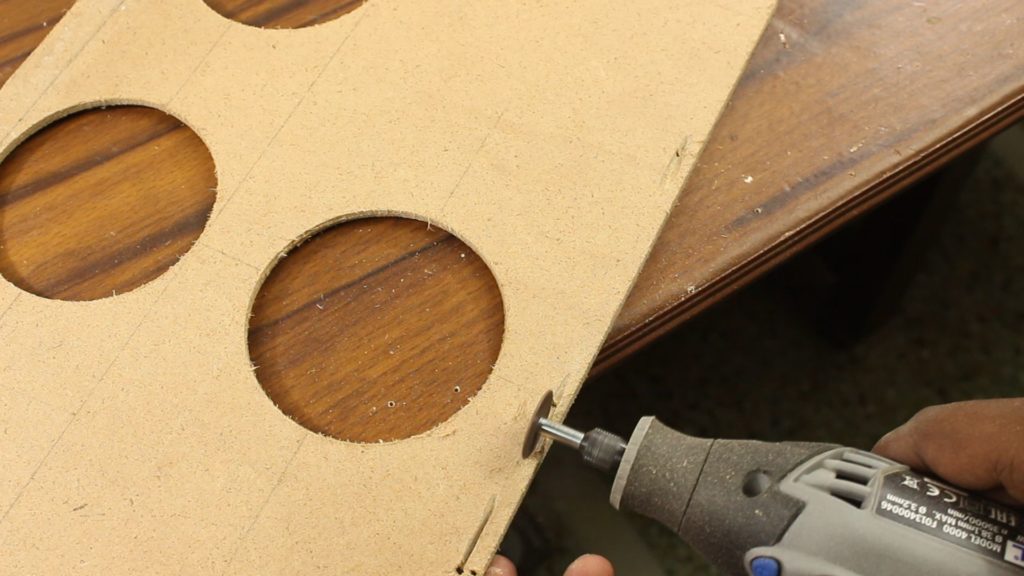
During the bending process, I have used a piece of plywood as a support to protect the MDF.
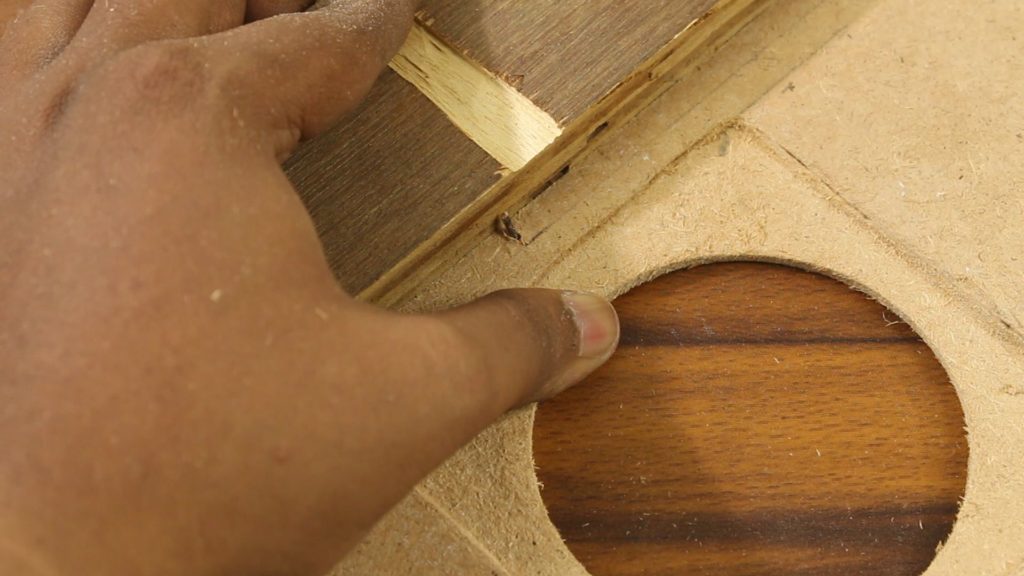
Next, for the screw mount, I took the original lid > mark its screw with this marking pencil > aligned the original lid on the MDF and rotate this screw to trace screw mark on it.
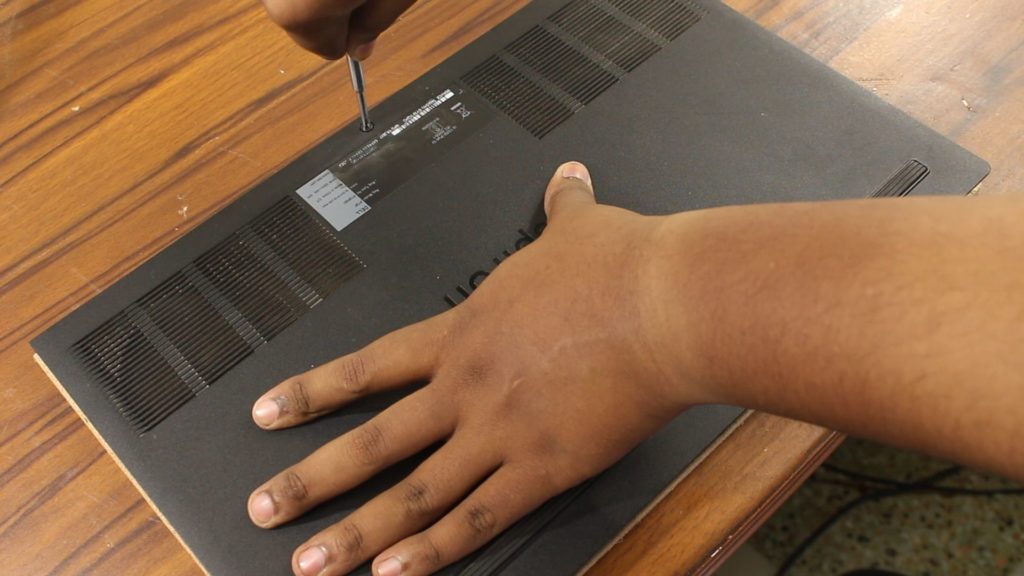
Don’t get me wrong; taking out the screw from its place is a pretty hard job to do and may destroy the screw and it’s locking mechanism. To fit the screw in place, first I have used a 1.5 mm drill bit then countersink in order to make a proper hole and finally a 6 mm drill bit to create the groove for the bolt.
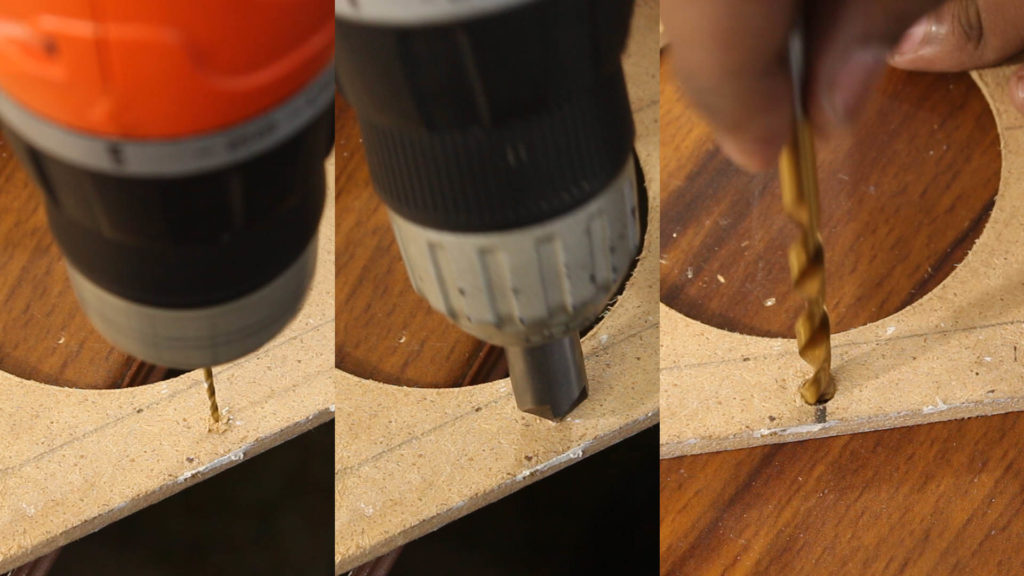
After setting the bolt inside, I put the screw through the hole which moves freely inside it and the screw head should not pass through it. Here, I am not mentioning the size of the screw and bolt because every laptop uses different screws so you have to find yourself what is suitable for you.
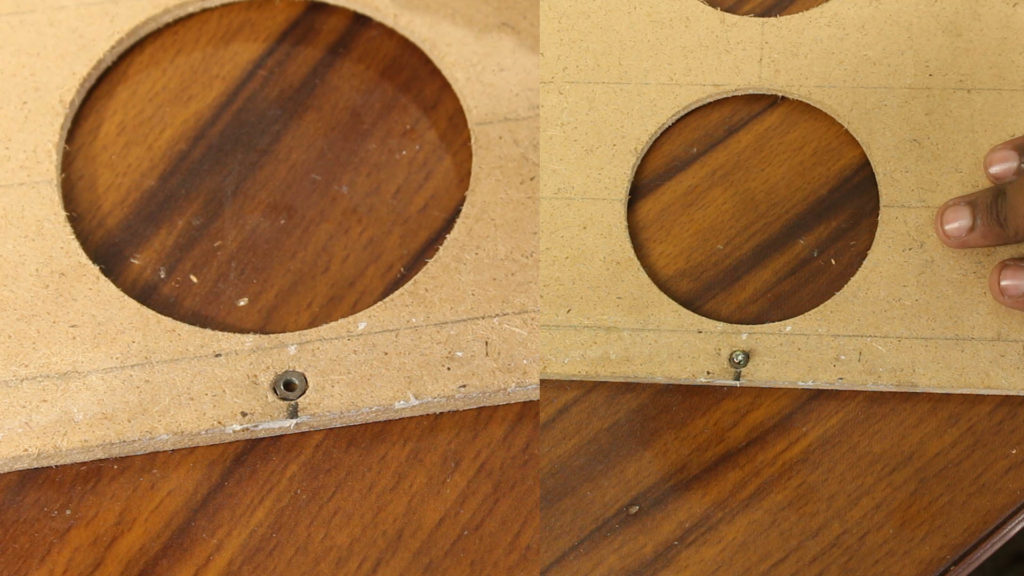
Ok, moving on, let’s check the design is working or not, thankfully it’s working. The back cover set properly inside its cavity and also because of that screw and hinge it will never fall out.

Time for Finishing Touch!
Ok, for the finishing touch, let’s disassemble all the accessories and use two-component adhesive to fix all of them in place.
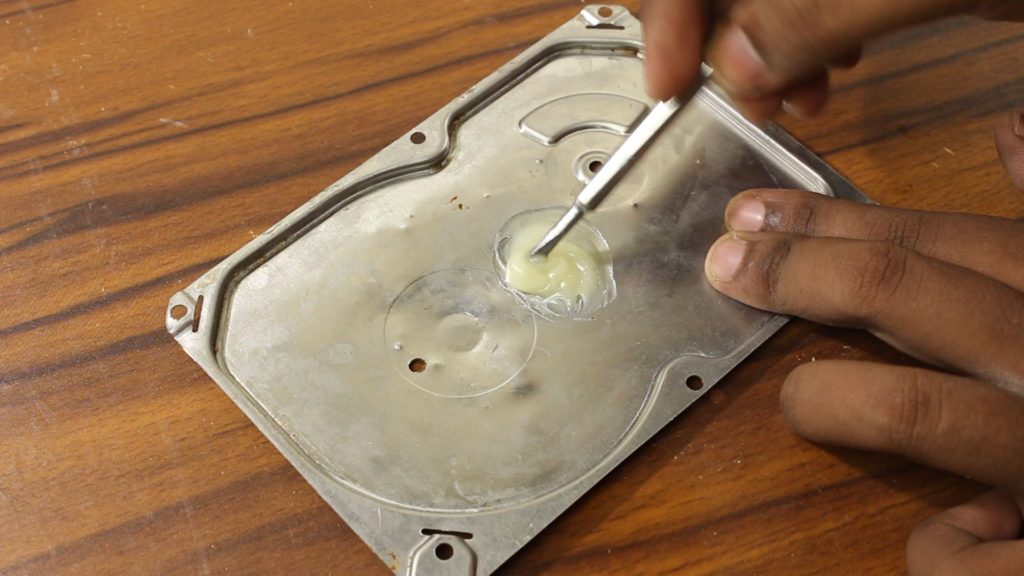
So, let’s start with the metal mesh. After applying the glue, I have placed the mesh and put some heavyweights on it.

After a day, the results are not pretty impressive to look at so, I have used some hot glue to set the fixture with the MDF.
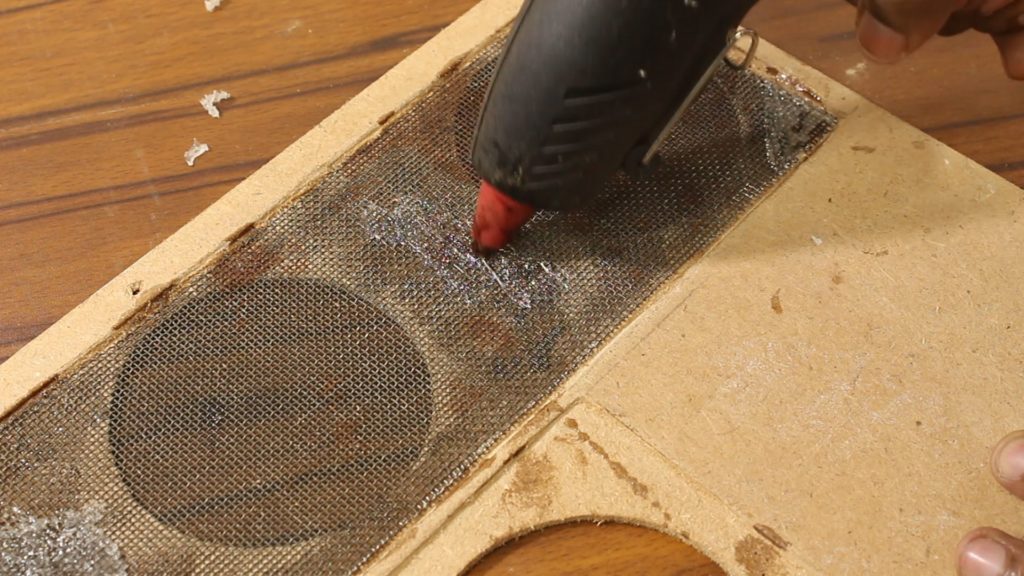
Then, by following the same procedure, I have placed the small one too.
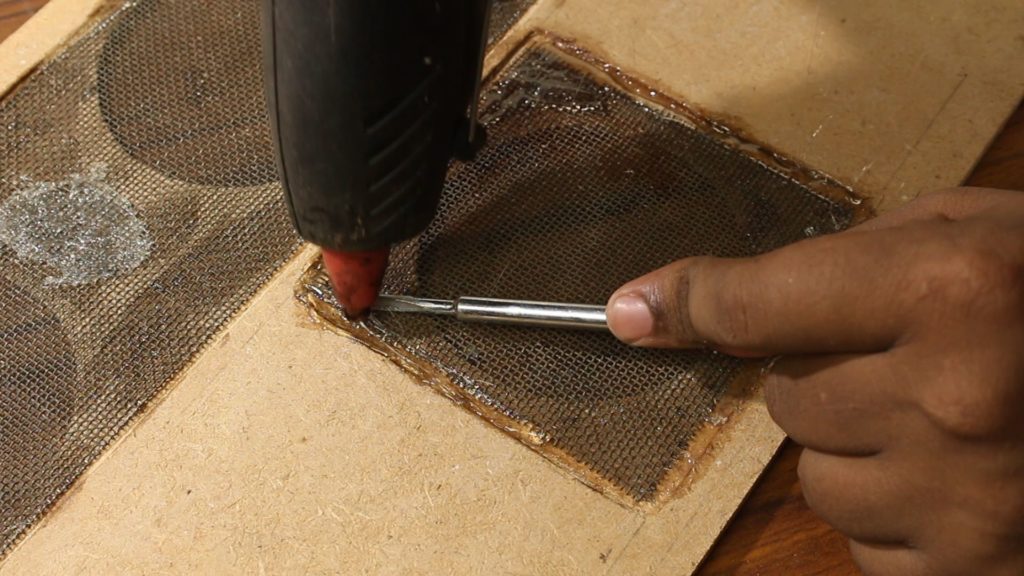
After an around 48 hrs. later, I have flipped the board > put the glue inside the cavities and place all the accessories in it.
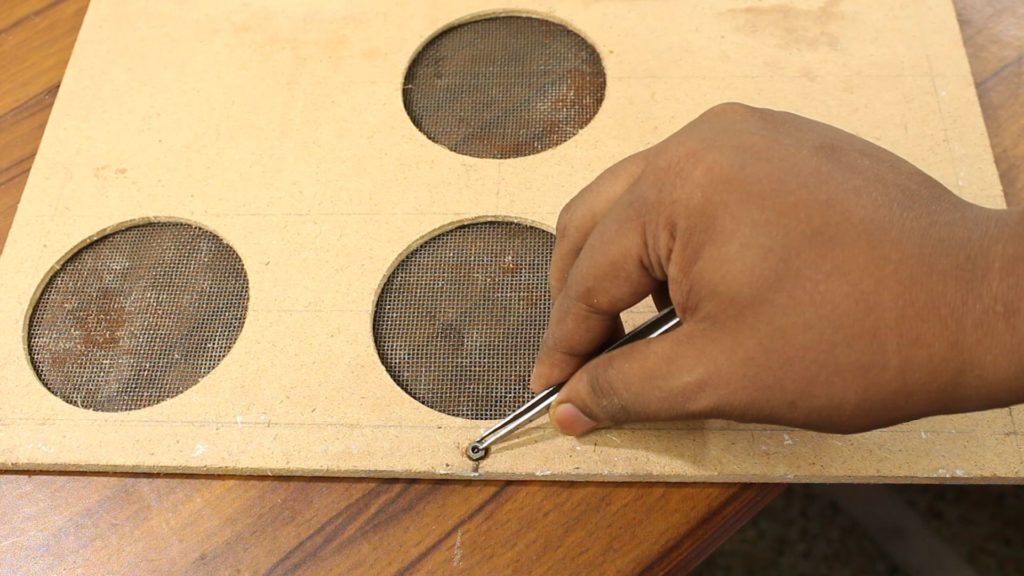
It is important after gluing the hinge I use the excess glue to cover up the groove and let it dry for 24Hrs.
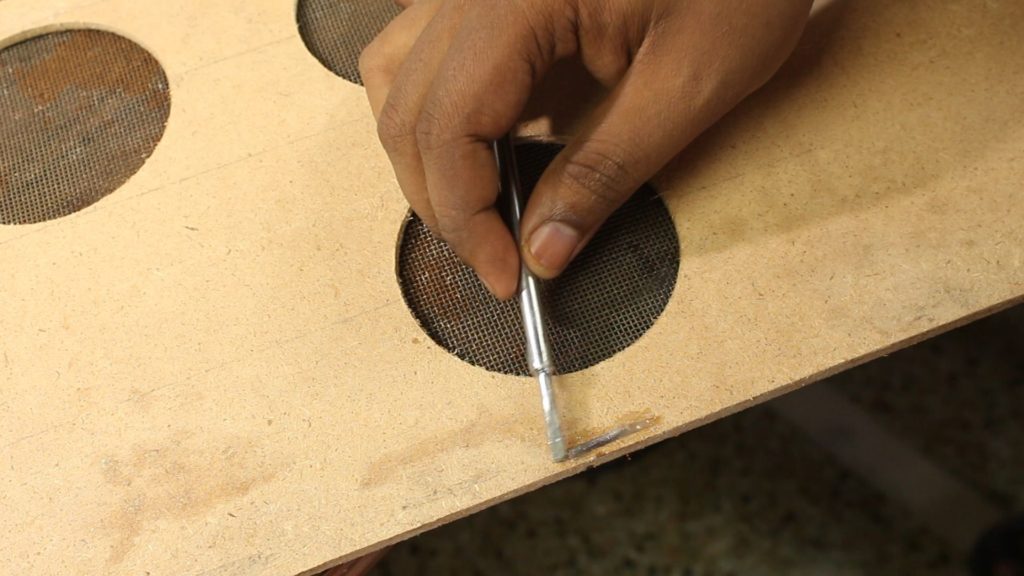
Next, I used grid 80 sand paper and sand down the surface. Now, we need to use some wood primer on it but I don’t have any so I have painted it and let it dry for 5 Hrs. then, I have applied another coat on it and keep it dry. after 24Hrs has passed, I got this result. Finishing Is not so perfect though but it should do its job fine later I think.
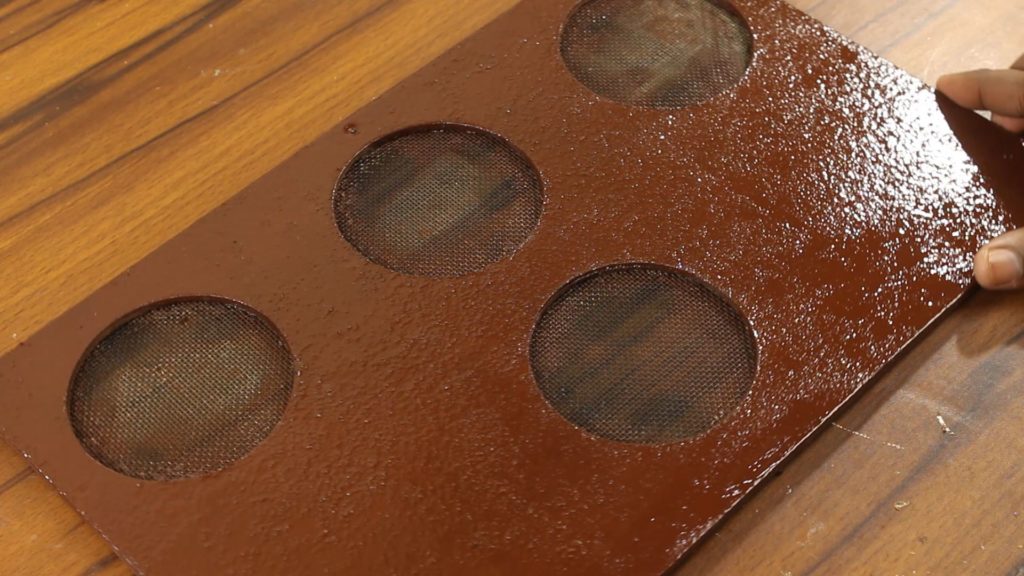
Time for Testing!
So, to test it, I have set this contraption with my laptop and started playing some games. In thermals, we can’t see any difference in it but the thermal throttling issue is solved.
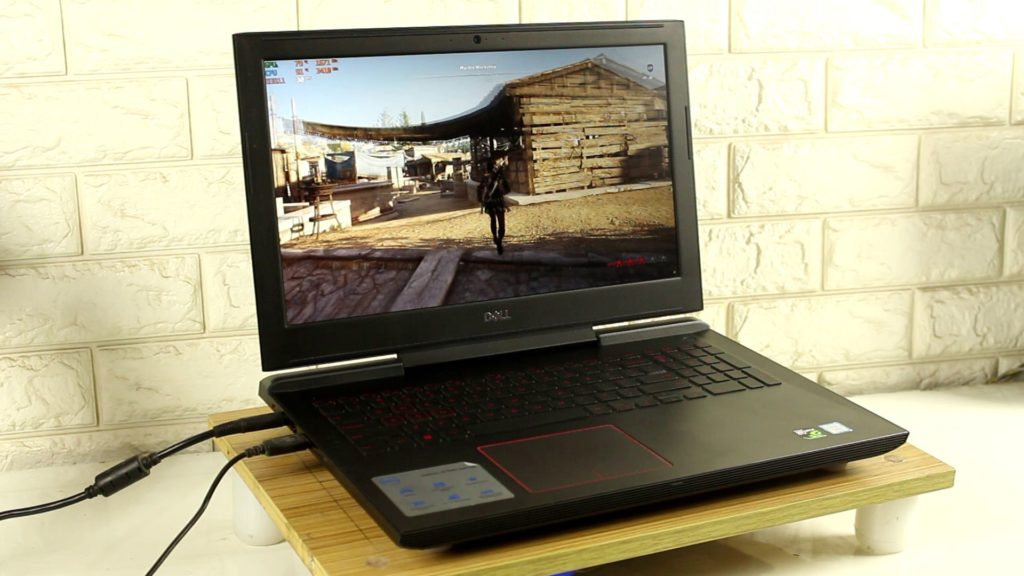
CPU and GPU both works above their base frequency, no underclocking, and nothing. so, it’s kind of success.
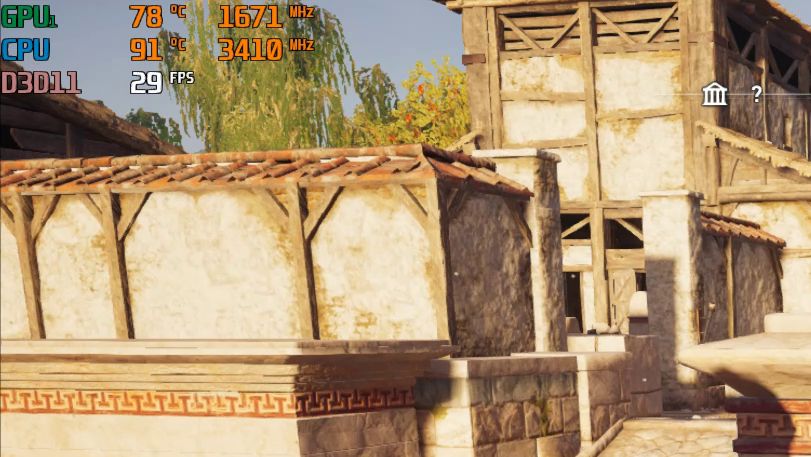
To protect the MDF and its color to wear out I have used some buffers with some double-sided tapes to stick it in place.
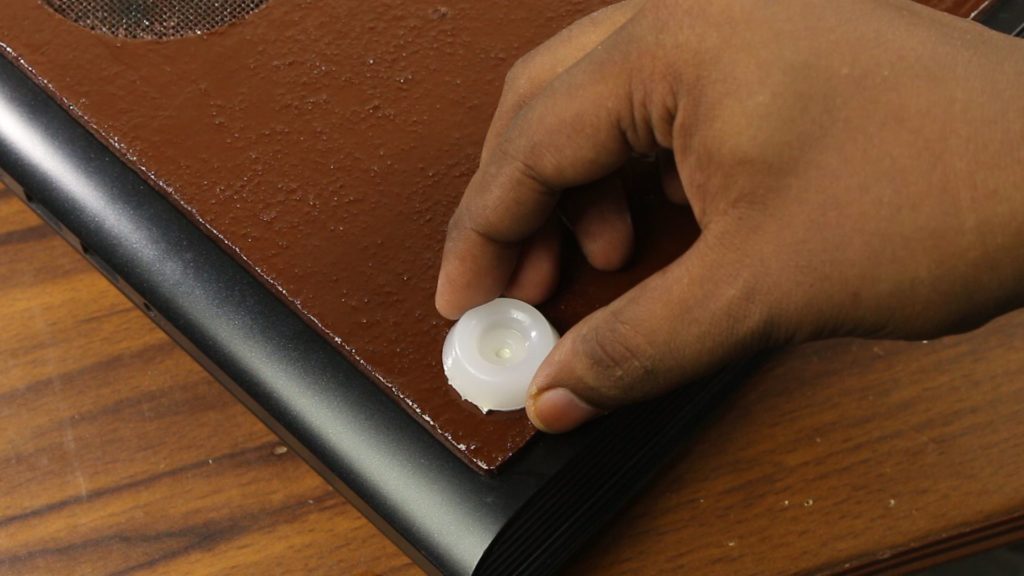
Does it Work?
Therefore, if you ask me that making of such a complicated thing is worth it or not then I can confidently say yes. With a good cooling pad such as my DIY one, this back cover works really well. I can play any AAA games without any lags due to thermals also I can edit videos and stuff without worrying about overheating so you can definitely make something like this. If you are planning to do so then you should check my video too. Click here to watch the video. Lastly, Hope you guys have understood & enjoyed “How to Cool Laptop Properly by Creating a Cooling Pad?” and it has really helped you to solve your problem. If so then don’t hesitate to express your valuable thoughts in the comment section below. Thanks for visiting and appreciating my work.